Calibration by means of comparison method
The comparison method, on application of which the calibrated vibration transducer is mechanically connected to the standard transducer (reference), is used in case of factory calibration of accelerometers. Based on apparatus of our enterprise, it is possible to create the automated system for the check of vibration transducers using the comparison method. Such systems are effective for laboratory calibration as well as for daily calibration of accelerometers.
The accelerometer, being calibrated by comparison method, i.e. the accelerometer, the sensitivity of which is subject to determination in the process of calibration, is mechanically connected to the accelerometer being used as the reference transducer, for example AP 10. The set, created in such a way, is fixed on the vibrating table of appropriate vibration stand, possessing the exactly determined parameters. As the calibrated and reference accelerometers, connected together, execute the mechanical vibrations with the identical acceleration, the ratio of amplitudes of electric signals, given by both accelerometers, is the ratio of sensitivity values, being incidental to them. Therefore, based on this ratio and calibrated value of sensitivity of the reference accelerometer it is possible to determine the search value of sensitivity of calibrated accelerometer.
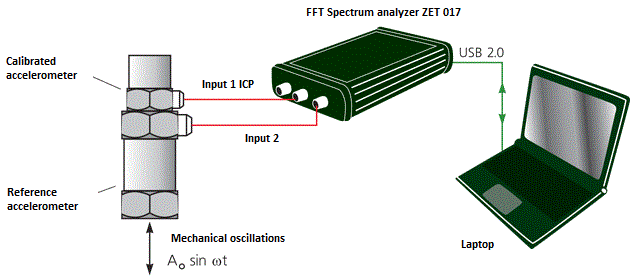
Figure 1
The simplest system for the calibration of accelerometers by comparison method is demonstrated in Figure 1. The mechanical vibrations with the sine waveform and specified acceleration amplitude and frequency are given to the calibrated and reference accelerometers, being mechanically connected together. The electric signals, given by these accelerometers, come on the spectrum analyzer, and the signal amplitudes are measured by electronic voltmeter, being the part of the software ZETLAB.
In the improved calibration system, created on the basis of above-described system, the signals from calibrated and reference accelerometers are amplified by corresponding pre-amplifiers, i.e. the charge amplifiers, during the determination of sensitivity according to the charge or by voltage amplifiers in case of calibration, performed for determination of sensitivity according to the voltage. The simultaneous processing of the signals, coming from calibrated and reference accelerometers, takes place in the process of calibration.
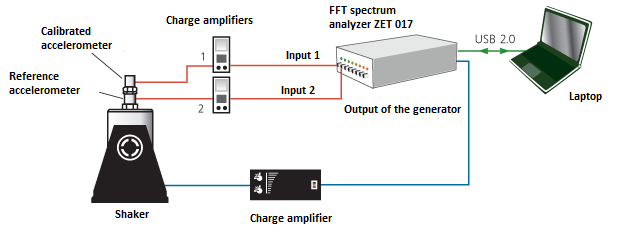
Figure 2
The application of the scheme in Figure 2 offers the following possibilities:
- simplification of comparison of amplitudes of the signals given by both accelerometers;
- reduction of time, being necessary for calibration;
- provision of overall tolerance, being comparable to the factory calibration tolerance;
- conversion of voltage to charge for determination of sensitivity according to voltage and charge.
The values of frequency and amplitude of acceleration of mechanical vibrations are usually defined by the standard or recommendation, being taken into account in the process of calibration. Usually the values of frequency and amplitude of mechanical vibration acceleration, being equal to 160 Hz and 100 m/s2 correspondingly, are taken as the reference values for the factory calibration. The provision of predetermined values of frequency and amplitude of acceleration of mechanical vibrations is not mandatory, if the values of these parameters, taken into account in the process of calibration, are within the normal working frequency and dynamic ranges of calibrated accelerometers. It is acceptable given that the piezoelectric accelerometers are the linear transducers, i.e. the vibration transducers, possessing the linear working frequency and dynamic ranges.
See also:
- Automation of the process of measurement of vibration-measuring converter parameters
- Vibration transducer calibration system on the basis of FFT Spectrum Analyzers